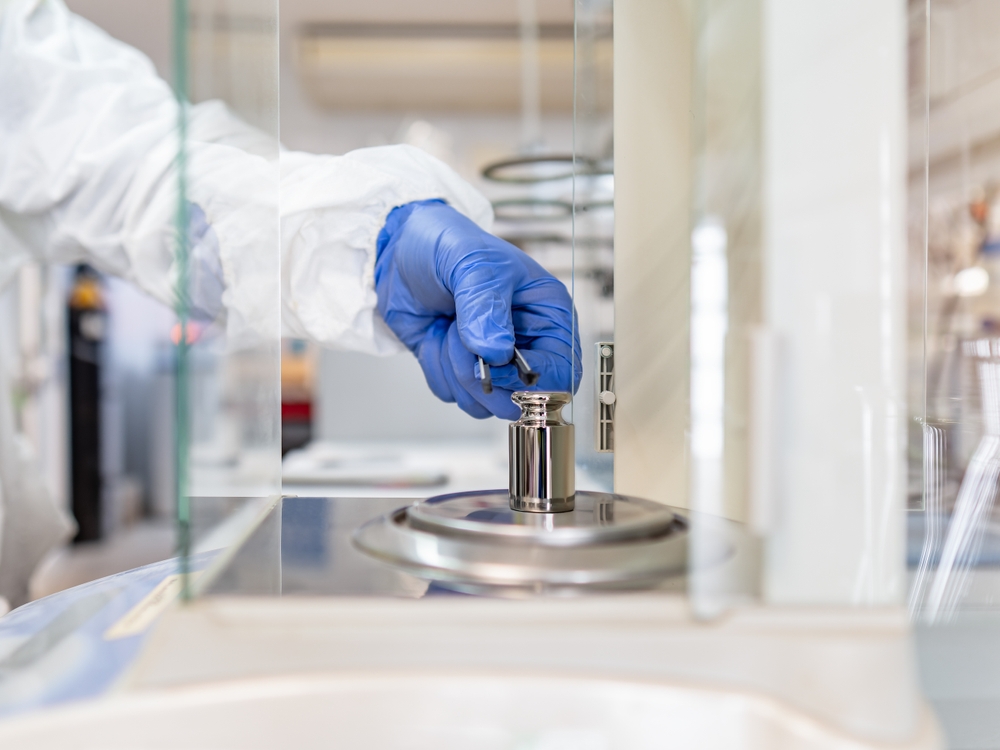
Lab Calibration Ensures FDA Compliance in Pharmaceutical Labs
At Cryostar Industries, located on Long Island, we understand that the backbone of pharmaceutical labs lies in precision and reliability. Ensuring FDA compliance isn’t just about meeting regulatory standards; it’s about safeguarding public health. This is a key focus of the FDA’s Current Good Manufacturing Practice (CGMP) regulations.
Pharmaceutical laboratories must adhere to strict regulatory standards to ensure the safety, efficacy, and quality of their products. One of the most critical aspects of maintaining compliance with the U.S. Food and Drug Administration (FDA) is the regular calibration of laboratory equipment. Without proper calibration, pharmaceutical labs risk inaccurate measurements, regulatory violations, and compromised drug quality. Here’s how regular calibration ensures FDA compliance and why it should be a priority for every pharmaceutical facility.
Understanding FDA Compliance
The Food and Drug Administration (FDA) sets stringent guidelines to ensure that pharmaceuticals are safe, effective, and consistent. Part of these guidelines includes the validation of processes, equipment, and methodologies used in pharmaceutical manufacturing and testing. Calibration is integral to this validation process, ensuring that all measurements are accurate and reliable.
The Role of Calibration in Accuracy and Reliability
Equipment calibration involves adjusting or setting measurement devices to ensure they provide accurate readings. In a pharmaceutical lab setting, this could mean calibrating:
- Analytical balances for precise weighing of substances.
- pH meters for accurate pH measurements in solutions.
- Temperature sensors used in stability chambers or autoclaves.
- Spectrophotometers for correct absorbance readings in drug concentration assays.
Without regular lab equipment calibration, even the slightest deviation can lead to significant errors in drug formulation, quality testing, or stability studies, potentially compromising patient safety and product efficacy.
FDA Requirements for Lab Equipment Calibration
The FDA’s guideline document, 21 CFR Part 211, explicitly mentions the need for equipment calibration as part of:
- Equipment Suitability – Instruments must be capable of producing reliable results.
- Control Procedures – Calibration checks should be part of routine maintenance to ensure equipment performs within specified limits.
Regular calibration not only meets these requirements but also provides documented evidence during FDA inspections, demonstrating due diligence in maintaining equipment standards.
The Role of Calibration in Pharmaceutical Lab Compliance
Equipment calibration involves adjusting or setting measurement devices to ensure they provide accurate readings, often traceable to national standards maintained by organizations like NIST. Regular calibration of laboratory equipment helps pharmaceutical companies meet FDA regulations in several key ways:
1. Ensures Accuracy and Reliability
Accurate data is critical in pharmaceutical research, production, and quality control. Instruments such as HPLCs, spectrophotometers, balances, and pH meters must be properly calibrated to prevent measurement errors that could impact drug formulation and safety.
2. Prevents Contamination and Cross-Contamination
Improperly calibrated temperature-controlled equipment, such as incubators and refrigerators, can compromise drug stability, leading to contamination risks. Regular calibration ensures that temperature-sensitive medications remain within specified conditions.
3. Maintains Batch Consistency
Pharmaceutical manufacturing relies on precise measurements to maintain batch-to-batch consistency. If a balance, pipette, or moisture analyzer is out of calibration, variations in ingredient amounts can lead to defective or non-compliant products.
4. Supports Audit Readiness
During FDA inspections, calibration records are among the first documents reviewed. A well-maintained calibration log demonstrates compliance, reducing the risk of regulatory action. Labs that lack proper documentation may face warnings or shutdowns.
5. Reduces Risk of Product Recalls
Errors due to uncalibrated equipment can lead to incorrect dosages, contamination, or stability issues, all of which can trigger costly product recalls and damage a company’s reputation. Regular calibration minimizes these risks.
Essential Lab Equipment That Requires Calibration
To maintain compliance, pharmaceutical labs should routinely calibrate the following equipment:
- Balances and Scales – Ensure accurate weighing of active ingredients.
- Pipettes – Maintain precision in liquid handling.
- HPLC & GC Systems – Guarantee accurate chemical analysis.
- Spectrophotometers – Ensure proper drug formulation and quality control.
- pH Meters – Maintain accuracy in acidity and alkalinity measurements.
- Temperature-Controlled Equipment (Incubators, Freezers, Refrigerators) – Protect drug stability.
- Dissolution Testers – Ensure consistency in drug release rates.
- Conductivity Meters – Maintain purity levels in water and solutions.
Benefits of Regular Equipment Calibration at Cryostar Industries
- Enhanced Data Integrity: Accurate calibration ensures that all data generated is reliable, which is crucial for batch consistency and regulatory submissions.
- Risk Mitigation: By identifying and correcting discrepancies early, calibration reduces the risk of product recalls or regulatory sanctions due to non-compliance.
- Operational Efficiency: Well-maintained equipment operates more efficiently, reducing downtime and extending the lifespan of the instruments.
- Compliance Assurance: Regular calibration schedules help in maintaining an audit-ready status, making compliance checks smoother and less disruptive.
- Cost Savings: Proactive calibration can prevent costly errors in drug production and testing, thereby saving resources in the long run.
Implementation at Cryostar Industries
At Cryostar, our calibration process is:
- Scheduled: We have a fixed schedule for calibration based on manufacturer recommendations, usage, and criticality of the equipment.
- Documented: Every calibration event is logged with details on who performed it, when, and the results, ensuring traceability.
- Verified: Post-calibration, we verify equipment performance against known standards or reference materials.
- Reviewed: Calibration records are regularly reviewed for compliance and improvements.
For instance, our high-performance liquid chromatography (HPLC) systems are calibrated not just for precision in retention times but also for detector response, ensuring the robustness of our analytical methods.
Conclusion
Regular calibration is not just a regulatory checkbox; it’s a commitment to quality and safety at Cryostar Industries. By integrating calibration into our daily operations, we ensure that our products meet the highest standards of quality and compliance, thereby reinforcing trust among regulators, healthcare providers, and patients.
Call for Immediate Lab Services |
---|
Long Island, Nassau & Suffolk County Call: 516-333-4006 |
The Bronx, Manhattan, Brooklyn, Queens, & Staten Island Call: 718-885-0833 |
Albany & Southern New York State Call: 800-564-5513 |
Piscataway, Northern & Central New Jersey Call: 800-564-5513 |
Danbury Connecticut & Surrounding Areas Call: 203-748-7343 |
24/7 Emergency Service |