Are you experiencing issues with your ultra-low temperature (ULT) freezer? As a Cryostar customer, you have access to our expert technicians who can diagnose and repair your lab equipment quickly and effectively. However, before you schedule a service call, you may want to check if the problem is something you can solve on your own. Here are five common ULT freezer problems and some tips on how to troubleshoot them.
1. High Temperature Alarm
If your ULT freezer is beeping or flashing a red light, it may be due to a high temperature alarm. This means that the temperature inside the freezer has risen above the set point, which could damage your samples or vaccines. To address this issue, first, check if the door is closed properly and the gasket is intact. Next, inspect the condenser coils and clean them if they are dirty or clogged. Finally, verify if the compressor is running and if the refrigerant level is sufficient. If none of these steps help, contact Cryostar for assistance.
2. Ice Build-up
Ice build-up inside the freezer can cause frost on the samples and reduce the cooling efficiency. To prevent this problem, make sure that the defrost cycle is functioning correctly, and the evaporator fan is running smoothly. If you see excessive ice, try to defrost the freezer manually by turning it off and letting it melt, or by using a hairdryer or a scraper (carefully!). Note that some models have an automatic defrost system that may take several hours to complete.
3. Water Leakage
Water leakage from the ULT freezer can be a sign of a clogged drain line, a faulty condensate pump, or a damaged water filter. To fix this issue, check the drain pan and remove any debris or ice. If the pump is not working, replace it with a compatible part or contact Cryostar for a replacement. If the water filter is dirty, replace it following the manufacturer’s instructions.
4. Noisy Operation
If your ULT freezer is making unusual noises, such as rattling, buzzing, or clicking, it could be due to a loose component, a worn-out fan motor, or a faulty thermostat. To troubleshoot this problem, first, inspect the interior of the freezer and tighten any loose screws or bolts. Next, check the fan blades and the motor for any damage or wear. If you notice any signs of wear, contact Cryostar for a replacement. Finally, test the thermostat by adjusting the temperature settings and monitoring the response.
5. Error Codes
Some ULT freezers have digital displays that show error codes when something goes wrong. To interpret these codes, refer to the user manual or contact Cryostar for assistance. Common error codes include “sensor failure,” “door open,” “power loss,” “communication error,” or “system fault.” Depending on the code, you may need to reset the freezer, replace a faulty sensor, or update the software.
Still Having Issues? What a Lab Equipment Repair Company Checks
Cryostar will typically check a number of key components when fixing an ultra-low temperature (ULT) freezer, as these freezers are critical to the proper storage of biological and pharmaceutical materials.
First and foremost, we will likely check the compressor, as this is the heart of the ULT freezer. Our technicians would ensure that the compressor is functioning properly and is free of any leaks or malfunctions. Additionally, they would check the compressor’s oil levels, as this is crucial to the compressor’s long-term operation.
Next, we would likely check the freezer’s evaporator coils. Evaporator coils are responsible for removing heat from the freezer’s interior. We will inspect the coils for any damage or corrosion, as well as ensure that they are properly cleaned and free of any blockages.
Other components that our lab equipment repair company would likely check include the freezer’s electrical system, temperature controls, and insulation. Our techs would ensure that all electrical connections are secure and functioning properly, that the temperature controls are calibrated correctly, and that the freezer’s insulation is intact and free of any damage or deterioration.
Overall, Crysotar would take a comprehensive approach to fixing a ULT freezer, as these freezers are critical to the proper storage of important materials and must be functioning at their best at all times.
Conclusion
In conclusion, ULT freezers are critical equipment for preserving valuable samples and vaccines, but they can also malfunction from time to time. By following these troubleshooting tips, you can save time and money on ULT freezer repairs and ensure the long-term performance of your Cryostar freezer. If you need further help, don’t hesitate to contact Cryostar for professional ULT freezer repair services.
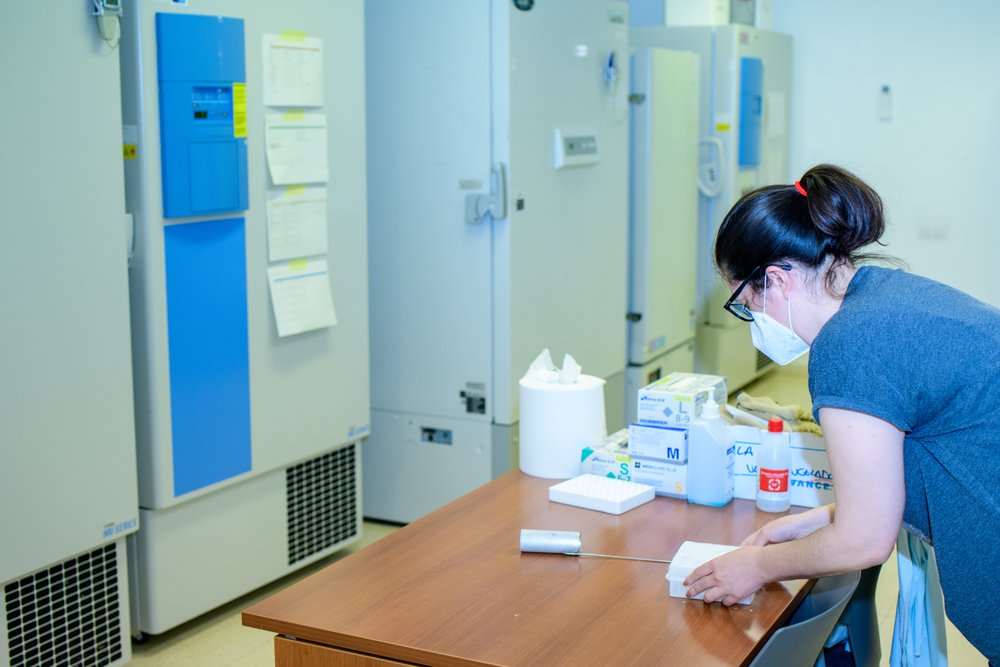
Call for Immediate Lab Services |
---|
Long Island, Nassau & Suffolk County Call: 516-333-4006 |
The Bronx, Manhattan, Brooklyn, Queens, & Staten Island Call: 718-885-0833 |
Albany & Southern New York State Call: 800-564-5513 |
Piscataway, Northern & Central New Jersey Call: 800-564-5513 |
Danbury Connecticut & Surrounding Areas Call: 203-748-7343 |
24/7 Emergency ServiceCall: 1-800-564-5513 |